Designing Compressed Air System
Compressed
air treatment, compressed air production
Designing a compressed air system
Size considerations
Installation costs
Installation instructions
Variables to consider
Energy savings
System Configuration
Corrosion
Durable protection of equipment
Air contamination
Air leaks
Designing a Compressed Air System
The Transair Connection Process
Labor accounts for 20 percent of the cost of
installing an aluminum piping system. By
comparison, labor accounts for 60 to 80 percent
of a steel system, 50 to 70 percent of a copper
system and 40 to 60 percent of a plastic system.
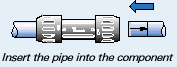
The
materials and modular design of a Transair air
quick connection pipe system makes it easier and
less expensive to install than traditional
systems. Its aluminum piping is easier to lift
and handle than standard steel piping, and its
push-to-connect fittings secure connections with
a simple push and twist. The fittings eliminate
the need for special tools, pipe preparation and
threading. The use of Transair also eliminates
the time needed for soldering and glue drying.
And once the pipe is pushed into the fittings,
the connections secure and ready to be
pressurized.
Size Considerations
A common error we see in compressed air systems,
in addition to poor piping practice, is line
sizes too small for the desired air flow. This
isn’t limited to the interconnecting piping from
compressor discharge to dryer to header. It also
applies to the distribution lines conveying air
to production areas and within the equipment
found there. Undersized piping restricts the
flow and reduces the discharge pressure, thereby
robbing the user of expensive compressed air
power. Small piping exacerbates poor piping
practices by increasing velocity- and
turbulence-induced backpressure.
Pipe size and layout design are the most
important variables in moving air from the
compressor to the point of use. Poor systems not
only consume significant energy dollars, but
also degrade productivity and quality. The
objective in sizing interconnecting piping is to
transport the maximum expected volumetric flow
from the compressor discharge, through the
dryers, filters and receivers, to the main
distribution header with minimum pressure drop.
Contemporary designs that consider the true cost
of compressed air target a total pressure drop
of less than 3 psi.
Beyond this point, the objective for the main
header is to transport the maximum anticipated
flow to the production area and provide an
acceptable supply volume for drops or feeder
lines. Again, modern designs consider an
acceptable header pressure drop to be 0 psi.
Finally, for the drops or feeder lines, the
objective is to deliver the maximum anticipated
flow to the work station or process with minimum
or no pressure loss. Again, the line size should
be sized for near zero loss. The lower the
pressure drop in transporting air, the lower the
system’s energy input.
^ Back To Top
Installation Costs
Transair compressed air pipe systems are quick
to install and ready for immediate
pressurization. No particular preparation
(cutting, deburring, chamfering, etc.) is
required. Transair aluminum pipe is calibrated
and fits perfectly with all Transair components.
Each connection is automatically secured and the
seal is optimized. Components are removable and
interchangeable and allow immediate and easy
layout modifications. All components incorporate
quick assembly connection that enables Transair
systems to be assembled much more quickly than
galvanized steel or copper system.
Example:
Galvanized installation: 6 feet per hour
Copper installation: 8 feet per hour
Transair installation: 45 feet per hour
All modifications add extensions to Transair
systems can be done extremely quickly and will
meet your production requirements.
Example:
Lateral dismantling of pipe: 1 minutes 30
seconds
Drilling of pipe: 2 minutes 30 seconds
Mounting Brackets: 45 seconds
Remounting of pipe to the system: 1 minute 30
seconds
Installation Instructions
General:
Prior to the installation of a Transair
compressed air distribution system, the
installer should ensure that the installation
area complies with any regulations applicable to
areas exposed to explosive hazards (in
particular the effect of static electricity in a
silo area). Transair should be installed
downstream of the compressed air receiver, or
after the dryer. Flexible Transair hose can be
installed at the start of the system in order to
eliminate any sources of vibration and to
facilitate maintenance operations. When
maintaining or modifying a Transair system, the
relevant section should be vented prior to the
commencement of any work. Installers should use
only Transair components and accessories, in
particular Transair pipe clips and fixture
clamps. The technical properties of the Transair
components, as described in the Transair
catalog, must be respected.
Commissioning the Installation
Once the Transair installation has been
installed and prior to pressurizing, the
installer should complete all tests, inspections
and compliance checks as stated in any contract
and according to sound engineering practice and
current local regulations.
Transair Pipe and Hoses
Transair pipe should be protected from
mechanical impact, particularly if exposed to
collision with fork-lift trucks or when sited in
an environment with moving overhead loads.
Similarly, rotation of the pipe and pipe
supports should be avoided. Transair pipe must
not be welded. Flexible Transair hoses should be
used in accordance with the recommendations of
the installation guidelines. Note: In certain
situations, Transair aluminium pipe may be
formed with a bend - please contact us for
further information.
Expansion / Contraction
Expansion and contraction of the system should
be calculated prior to installation. The system
designer and installer should calculate the
elongation or retraction of each Transair line
according to the recommendations in this
installation guide.
^ Back To Top
Component Assembly
Transair components are provided with assembly
instructions for their correct use - simply
follow the methods and recommendations stated in
this document.
Situations to Avoid:
Installation within a solid mass (concrete,
foam, etc.)
The hanging of any external equipment to
Transair pipe
The use of Transair for earthing, or as a
support for electrical equipment
Exposure to chemicals that are incompatible with
Transair components (please contact us for
further details)
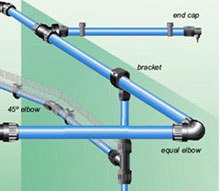
Variables to consider
^ Back To Top
Successful operations need to be able to take
advantage of new equipment options and
automation techniques without incurring lengthy
downtime and expense. Consequently, the ability
to reconfigure production layouts or implement
process changes quickly is critical. Transair
makes reconfiguration practical and efficient.
Because Transair’s fittings are not soldered or
glued, the components are reusable and can be
removed and reinstalled. The modular design and
handling ease enable plant personnel to
implement many layout changes within minutes,
not hours. This minimizes downtime and increases
plant productivity. Furthermore, the flexible
hose used in a Transair pipe system eliminates
many of the layout constraints encountered with
rigid piping systems such as physical obstacles.
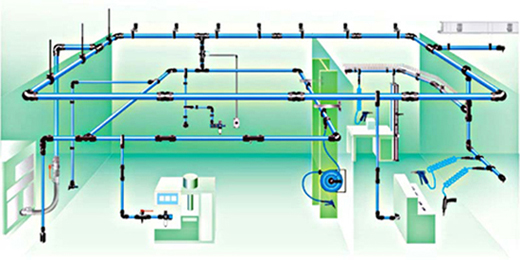
Energy savings
^ Back To Top
Energy costs associated with a compressed air
system are significant. For example, when
analyzed over a ten-year period, the cost of
energy consumed by an average compressed air
system exceeded other costs, including the
initial cost of equipment and installation. The
cost of electric may exceed the cost of the
capital equipment, each year! System pressure
drops are one cause of inefficient energy use. A
14.5 psi pressure drop uses 10 percent
additional energy. These drops can result from a
number of sources, including poor system
configuration, interior pipe surface corrosion,
and compressed air contamination.
System configuration
^ Back To Top
Poor system configuration can lead to improper
airflow. The flexible hose used in Transair
aluminum piping system eliminates many of the
layout constraints encountered with rigid piping
systems. It accommodates physical obstacles and
provides a link between the compressor and
piping.
Corrosion ^ Back To Top
Interior pipe corrosion is a common cause of
pressure drops and higher maintenance costs.
Smooth bore piping, such as plastic and
aluminum, resist corrosion. Galvanized and black
iron pipe decreases in opening over time.
Galvanized and black iron fittings are crudely
designed with restrictions to air flow
internally. Brass and copper fittings and valves
typically have smaller bores than the associated
pipe size. Transair pipe will not corrode and
the fittings are ALL designed for compressed air
flow with full bore construction.
Durability of equipment
^ Back To Top
Transair enables elimination of the problem of
rust, usually associated with steel air pipe
systems. It guarantees the complete absence of
corrosion (self protection by formation of
aluminum oxide). The inner surface of aluminum
pipe ensures good and constant quality clean air
continuously.
Legris Transair also protects industrial
equipment against water deterioration thanks to
its quick assembly brackets with integral upward
loop.
Compressing ambient air to the discharge
pressure introduces moisture into supplied air.
Unfortunately, aftercoolers, filters, and dryers
do not completely eliminate moisture and its
destructive results. As a result, steel pipe
systems will begin to rust and corrode, thereby
inhibiting smooth airflow and reducing system
pressure.
Pipe corrosion also increases compressed air
system maintenance. Steel pipe systems need to
be dismantled and inspected to monitor corrosion
build up. Not only does replacing corroded pipe
interfere with production, it causes rust,
corrosion and other particles to be released
into the air system, thereby causing instrument,
valve, tool and machine operation problems or
damage with the resultant downtime.
Air contamination
^ Back To Top
Air cleanliness is another factor that affects
consistent airflow. Dirt and dust particles
passing through the piping system are gradually
deposited on the interior surface of piping. As
these deposits accumulate, friction increases
and system pressure decreases. Black iron and
galvanized steel piping systems are more prone
to build-up than stainless steel. Meanwhile,
smooth bore piping materials, such as Transair
aluminum pipe, offer more resistance to deposit
build-ups.
Air leaks ^ Back To Top
Inherent in threaded steel piping systems, non
productive leaks also waste compressed air, thus
electrical energy and your dollars. Difficult to
trace and repair, they can have a huge impact on
operating budgets. A typical threaded compressed
air system leaks 35% of its volume, that’s one
third of the electrical bill associated with
compressed air! With its bubble-tight seals,
pipe and push to connect fittings will eliminate
compressed air leaks and lower your electrical
costs associated with the production of
compressed air.
Improving productivity while reducing operating
costs is a goal shared by nearly every
manufacturing plant. You cannot buy compressed
air, you must produce it. The initial capital
cost of a compressed air system is minor
compared to the operational cost. A Transair
aluminum and stainless steel pipe system will
significantly reduce your operational cost!
Transair aluminum piping system offers virtually
leak-free performance. Legris Transair
guarantees the Transair pipe system to be free
of leaks for two (2) years. The Transair
aluminum pipe and push to connect fittings will
eliminate compressed air leaks and lower your
electrical costs associated with the production
of compressed air.
|